Policy Landscape Shaping Epoxy Formulation in 2025
Federal VOC and Chemical‑Safety Rules
The U.S. Environmental Protection Agency tightened national emissions limits on volatile organic compounds for consumer and professional adhesives under its 2025 revision of the National Emission Standards for Hazardous Air Pollutants (NESHAP) for Epoxy Resins Production, capping total VOC content for two‑part epoxies at 100 g /L for interior use. Compliance is mandatory for all formulations marketed after March 2025.
Complementing the VOC cap, OSHA’s 2024 revision to the Hazard Communication Standard (aligning with GHS Rev 7) requires expanded pictograms, harmonized hazard statements, and updated 16‑section Safety Data Sheets for epoxies containing reactive diluents or amine hardeners. Labels must now flag skin‑sensitization Category 1 or 1A hazards in fonts ≥6 pt for quart‑size containers and larger.
State‑Level Rules: California Leads, Others Follow
California’s Consumer Products Program has pushed even lower VOC thresholds—70 g /L for non‑structural stone fillers sold at retail—as part of its 2025 Airborne Toxic Control Measure update. Manufacturers can use the Alternative Control Plan (ACP) only if they demonstrate emissions averaging across product families.
Several Northeast states adopt essentially identical limits through the Ozone Transport Commission model rule, while Washington and New York add Extended Producer Responsibility (EPR) surcharges on high‑VOC products to fund recycling of leftover chemicals.
International Factors: BPA and Beyond
If you export or import fillers, note the EU ban on bisphenol A (BPA) in epoxy food‑contact materials effective 20 Jan 2025; many suppliers have removed BPA entirely from new resin systems to avoid dual inventories. Canada and Australia reference the same hazard classes under their own REACH‑like frameworks, so a single BPA‑free, low‑VOC formula now covers most developed markets.
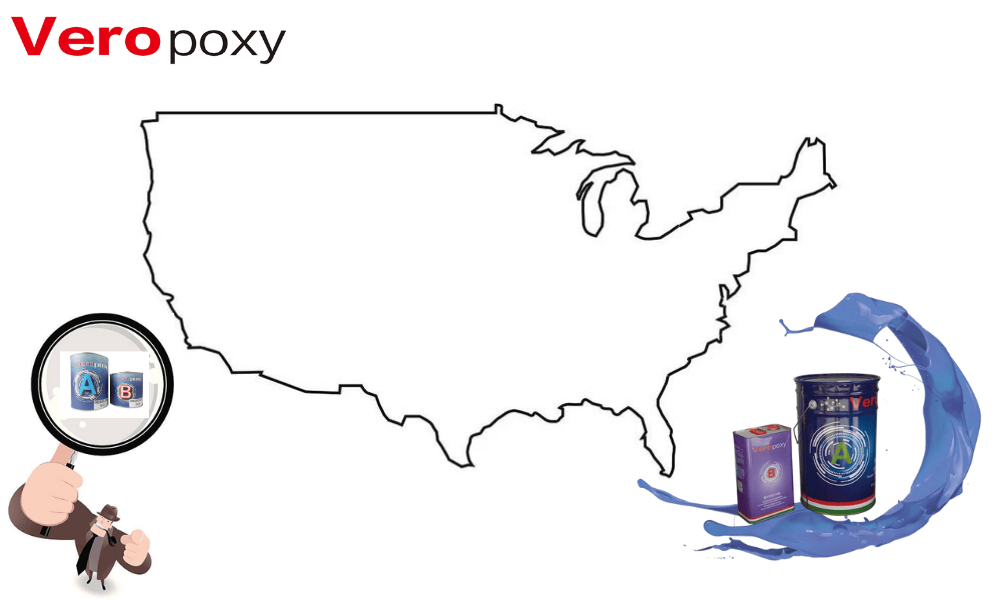
Epoxy Resins
Travertine and Epoxy: Technical Fundamentals
Why Choose Epoxy for Travertine?
Travertine’s open pores demand a travertine repair epoxy with ultra‑low shrinkage (<1 %) to avoid post‑cure dimpling. Epoxy for Travertine achieves compressive strengths exceeding 9 000 psi and water absorption below 0.1 %, sealing the stone against wine, oil, and household acids.
A premium color‑matching epoxy incorporates micro‑pigments ground to <5 µm, allowing exact tone replication. Veropoxy’s in‑house spectro‑scan service builds a custom pigment recipe within 48 hours so the filled area remains invisible under both warm and cool lighting.
Standards and Testing Benchmarks
All professional fillers must pass ANSI A118.3 shear‑bond and water‑cleanability tests—originally designed for ceramic tile but now referenced in the 2024 International Building Code for dimension stone repair. For exterior façades, select a UV‑resistant epoxy that meets yellowing index ΔE < 5 after 1 000 h Q‑Sun accelerated exposure (ISO 4892‑2).
Designing Epoxy Systems for Modern Compliance
Low‑VOC Formulations and Green‑Building Credits
To meet California’s 70 g /L limit and qualify for LEED v5’s Low‑Emitting Materials credit, Veropoxy reformulated its flagship filler into a low‑VOC stone adhesive using water‑borne reactive diluents and bio‑based polyols. Project teams using Veropoxy LV can claim up to two LEED points on indoor air quality.
BPA‑Free and Labeling Innovations
By substituting bisphenol F diglycidyl ether for BPA, Veropoxy avoids future EU and U.S. restrictions while maintaining the chemical backbone’s high glass‑transition temperature—critical for temperature‑resistant epoxy in hot‑climate façades. New QR‑coded labels provide instant SDS downloads, aligning with OSHA’s electronic‑access requirement.
Worker Safety and Ergonomics
The 2024 OSHA rule also introduces prescriptive glove standards. Nitrile (≥ 8 mil) or laminated film gloves are now obligatory when handling aminated hardeners, and employers must document fit‑testing at least annually. Veropoxy’s “E‑Cure” hardener emits <0.1 ppm ammonia, easing compliance with indoor short‑term exposure limits.
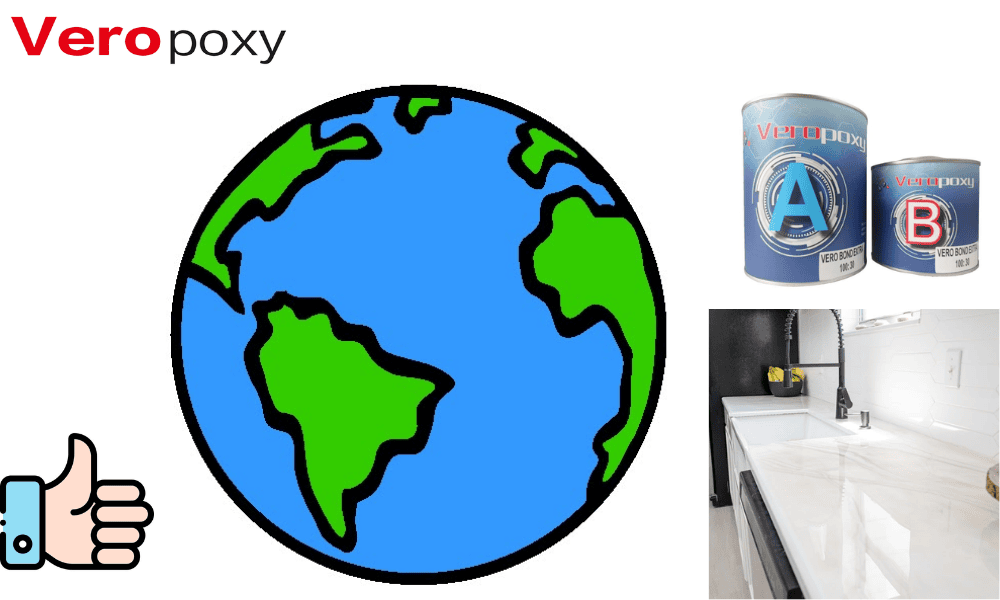
Best-selling Epoxy Resins
Application Best Practices Under the 2024/2025 Codes
Surface Preparation and Environmental Controls
-
Maintain ambient temperature 18–27 °C; relative humidity <70 %.
-
Vacuum pores, then flush with isopropyl alcohol to remove dust without leaving water that could inhibit cure.
-
Mix fast‑curing resin and hardener by weight (±2 %) to maximize high‑strength bonding; avoid volumetric ratios that can deviate up to 5 % in low‑viscosity systems.
-
For vertical repairs, choose a thixotropic flexible stone adhesive—thix index ≥3—preventing slump on risers or edges.
Indoor Air and Waste Management
Enclose large filling operations within temporary poly sheeting; vent negative‑pressure fans through 13‑ply pleated filters (MERV 14) to capture any aerosolized resin dust. Collect cured drips and packets for solvent‑free disposal under EPA Category D non‑hazardous solid waste if free of BPA.
Market Trends and Opportunities
Growing consumer demand for natural‑look surfaces, coupled with 2025 policy drivers, has propelled the market for eco‑friendly epoxy fillers by 8.5 % CAGR. Designers now specify “pore transparency” as a purchasing criterion—driving uptake of Veropoxy’s pourable filler that mimics the host stone’s translucency.
Insurance underwriters increasingly request proof of code‑compliant adhesive selection before covering multi‑story stone façades. Forward‑thinking contractors that adopt compliant Epoxy for Travertine not only reduce liability but also gain a marketing edge with sustainability‑conscious clients.
Frequently Asked Questions
Q: How many VOC grams per liter can my epoxy contain in California after July 1 2025?
A: Non‑structural stone fillers must be ≤ 70 g /L; structural bonding epoxies ≤ 100 g /L. Products above those limits must join CARB’s alternative compliance plan or be restricted to out‑of‑state sales.
Q: Will the EU BPA ban affect domestic projects?
A: Yes—U.S. importers of BPA‑containing epoxies may face supply disruptions. Selecting a BPA‑free Epoxy for Travertine now future‑proofs both domestic and export work.
Q: Can I still use solvent wipes for cleanup?
A: Only if the solvent itself meets local VOC limits (<25 g /L in many jurisdictions) and all wipes are sealed in approved containers prior to landfill.
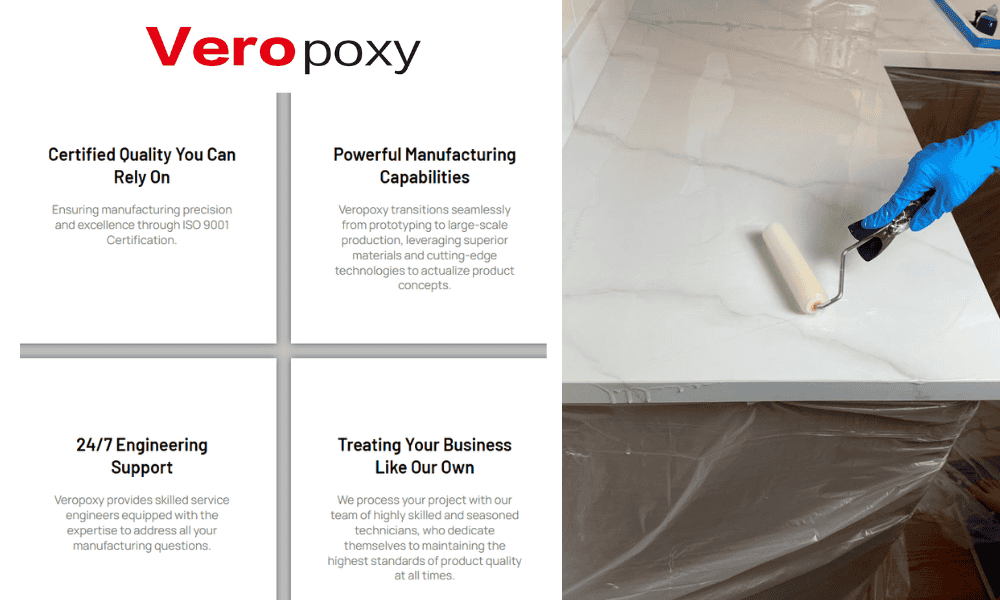
Epoxy for Travertine Suppliers
The convergence of stricter VOC caps, global chemical bans, and updated workplace‑safety standards has transformed stone repair from a purely technical exercise into a multidisciplinary challenge—one where chemistry, policy, and craftsmanship intersect. By choosing Epoxy for Travertine systems engineered for 2025‑level compliance, you protect workers, safeguard indoor air, and keep projects eligible for the latest green‑building credits.
Veropoxy’s formulations—BPA‑free, UV‑resistant epoxy blends with fast‑curing resin options—demonstrate that environmental responsibility and performance can coexist. As state regulations continue to leap ahead of federal rollbacks, and international markets tighten chemical‑safety nets, professionals who adapt early will not only avoid disruption but unlock new opportunities: premium service offerings, brand differentiation, and long‑term client trust.
The path forward is clear—embrace innovative, policy‑aligned stone adhesives today, and your travertine installations will stand the test of time, regulations, and environmental scrutiny alike.
Post time: 7 月-01-2025